阀门测试四个测试和评估级别是:
级别 1 – 不使用仪器的部分行程测试;
2 级 – 带有事件计时的部分行程测试;
3 级 – 使用基于执行器的仪器 部分和全行程测试(例如,控制信号、压力和位置反馈);
4 级 - 使用外部状态监测系统进行部分和全行程测试,包括 3 级参数,结合过程系统和基于阀门的测量(例如扭矩/推力和声泄漏检测)。
阀门测试在 2017 年更新开发过程中进行的分析表明,随着实施级别的提高,验证测试覆盖率显着增加。导致当前更新的讨论表明,1 级可能是最广泛使用的自动阀门测试方法。然而,这是最不有效的。在 1 级测试期间,阀门仅循环部分行程距离;记录的唯一测量是阀门是否移动。各种论文、技术报告和小组委员会参与者的意见表明,1 级实施提供了最低级别的校对测试覆盖率。
故障原因 图1、 五种原因应占故障的三分之二以上。
2 级方法使用仪器来测量阀门在两个已知位置之间移动所需的时间。当一切保持不变(例如系统压力、执行器压力、螺线管响应等)时,阀门行进已知距离并返回所需时间的变化可用于检测裕度的变化。这些附加信息通过揭示一些与裕度相关的降级来增加测试覆盖率。重要的是要注意最终用户必须为周期时间变化制定有意义的验收标准,以确保这种方法尽可能有效。
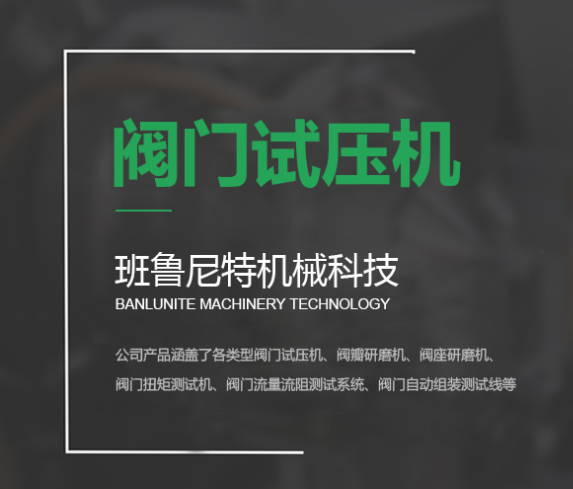
3 级方法是一些阀门控制器的内置功能,例如位置变送器和定位器。最终用户寻找执行器仪表提供的控制信号、压力和位置之间关系的变化,以评估表明裕度下降的变化的性能。 3 级方法对于双作用驱动器非常简单,但单作用弹簧复位驱动器也受到其他不确定性的影响。额外的不确定性源于执行器弹簧提供的关闭力,而不是可测量的压力。
Level 4 集成了安装在阀门和执行器上的传感器和数据采集设备,但与控制系统保持分离。这通常包括扭矩或推力工具、压力传感器、位置变送器和声学设备,用于在阀门关闭时检测泄漏或流量。第 4 级方法虽然比其他方法更昂贵,但提供了最高级别的验证测试覆盖率,降低了按需失败 (PFD) 的概率,并使安全目标更容易实现。